- Primera reunión plenaria de la Mesa de Desarrollo Integral de Pataz concluye con importantes acuerdos
- Ministro Jorge Montero: 31,560 pequeños mineros y mineros artesanales continuarán en el proceso de formalización
- MINEM: Nuestra meta es tener unidades productoras saneadas en la pequeña minería y minería artesanal
- Más de 1,000 mineros reciben asistencia para seguir proceso de formalización en Puno, La Libertad, Ica, Lima y Madre de Dios
- Remediación de Pasivos Ambientales iniciará en 4 nuevos sitios de la Amazonía
Mina digital: la revolución de los procesos mineros
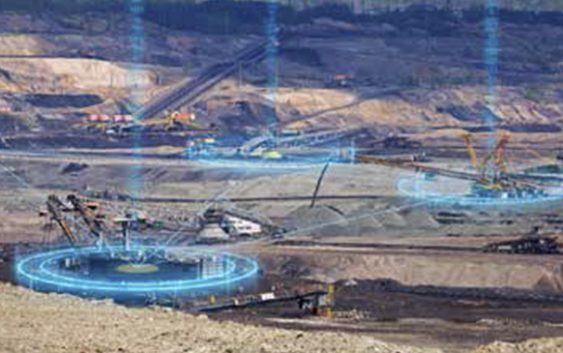
Las empresas relacionadas al rubro minero usan el término “Mina Digital” para sumarse a las nuevas tendencias industriales y no quedar fuera de la moda de marketing que este término provee. El concepto de mina digital no es sólo Internet de las Cosas e integrar un equipo a una “nube” en un servidor global. El concepto de mina digital global encierra una posibilidad sin precedentes para aplicar enfoques nuevos a los retos de siempre, para cambiar y revolucionar los procesos mineros actuales.
Con el profundo conocimiento del desarrollo de proyectos mineros, nos enfocamos en lograr una mina inteligente segura, eficiente en la utilización de recursos y enfocada en la reducción de costos, a través de la aplicación consistente y disciplinada de hogarunico.es kamagra conceptos como el de la mina digital y las herramientas que la componen. Todas estas herramientas en una sola plataforma integrada: Software de ingeniería COMOS, sistema de control descentralizado (DCS)SIMATIC PCS7 y el software SIMIT de simulación virtual.
Con herramientas como el software COMOS, Siemens es el único proveedor a nivel mundial que lleva a cabo proyectos integrados de gestión de activos de planta durante todo el ciclo de vida de una Mina, lo que permite trazabilidad y evita sobre costes en las etapas de transferencia entre ingeniería de proyecto a ingeniería de construcción, de operaciones a mantenimiento y a optimización física y virtual.
El concepto de mina digital global encierra una posibilidad sin precedentes para aplicar enfoques nuevos a los retos de siempre, para cambiar y revolucionar los procesos mineros actuales.
La integración de soluciones se lleva a cabo con el uso de protocolos como PROFINET que se basan en estándares de TI acreditados (Ethernet) y ofrece funcionalidad de TCP/IP completa para la transferencia de datos en toda la planta y a todos los niveles. Además, los usuarios gozan de las ventajas de los diagnósticos integrados y las comunicaciones de seguridad positiva, que ofrecen una disponibilidad óptima del sistema, que abarca desde los conceptos de máquinas modulares para conseguir la máxima flexibilidad hasta las velocidades de transferencia más rápidas y aplicaciones WLAN. En su conjunto, estas capacidades ofrecen un rendimiento considerablemente superior y si se adicionan las funcionalidades redundantes, la confiabilidad del sistema que integren no tiene comparación.
La revolución se logra con la optimización del uso de los recursos y esto se basa en la integración de una serie de soluciones inteligentes que permiten la obtención de datos y la configuración de los elementos de manera centralizada y remota. Esto es parte del concepto modular del portafolio SIEMENS. Por ejemplo, los relés de protección para subestaciones y control de redes de energía inteligentes SIPROTEC5, los módulos SIMOCODE para el manejo y gestión de centros de control de motores y accionamientos de Media y baja Tensión de la línea SINAMICS.
Toda esta información obtenida es concentrada en el DCS SIMATIC PCS7 donde, según el perfil y rol del usuario, se generan interfaces que le permiten a éste visualizar la información relevante de manera gráfica y sencilla, representando el proceso, perfilando el rendimiento, mostrando las variables principales de seguridad de los equipos, sus consumos e impactos en la producción y consumo energético.
Usando SIMIT se puede lograr el Gemelo Digital, tomando datos del DCS obtenidos de los procesos físicos en la mina, y permitiendo replicar la operación de la mina en un ambiente virtual en el cual se puede modelar distintos escenarios para analizar resultados sin alterar la producción de la mina y sin generar riesgos de paradas no programadas por algún fallo técnico que no se hubiese tenido en cuenta en una forma tradicional. Otr
a de las ventajas del SIMIT permite entrenar y preparar al personal técnico de forma segura en distintos escenarios virtuales, reduciendo costos y tiempos muertos en las paradas ya que el personal está familiarizado con las acciones a tomar.
El concepto Mina Digital permite integrar nuevas variables como las entregadas por el sistema SIMINE MAQ, que consiste en la detección en tiempo real de la calidad del material que pasa por las fajas transportadoras principales y que es mapeado y modelado. Con el modelamiento del “stock pile” se puede preparar con anticipación la planta para una campaña específica, y optimizar el consumo de reactivos, bolas de proceso y aumentar la recuperación, reducir el consumo energético, etc.
Al conocer con mayor precisión el material a procesar, ahora el foco está en mantener la oportunidad de procesar ese material a tiempo. Es en este momento cuando entran a participar otras herramientas digitales como el SIMINE AHA (Asset Health Analytics) en aplicaciones críticas como molinos y fajas de alimentación de material. SIMINE AHA toma las variables críticas de operación de los accionamientos de molinos y faja, generando huellas de operación en condiciones variables y creando un mapa operativo de los equipos. El SIMINE AHA utiliza inteligencia artificial para comparar variables, genera proyecciones en la operación y predice variables de comportamiento predeterminadas para los equipos. Esto permite distanciar las paradas de mantenimiento programado y predice la confiabilidad de los escenarios probados en el gemelo digital de la planta, reduciendo la incertidumbre de operación.
Así, el concepto de Mina Digital de Siemens permite la integración de productos, sistemas, soluciones y herramientas del portafolio Siemens y de terceros, con el objetivo final de aumentar la disponibilidad de la planta para procesar material de manera oportuna y así cumplir las metas de producción establecida para la mina.
José Amorós
KEY ACCOUNT SALES
PROFESSIONAL SIEMENS
SIEMENS es una empresa asociada a