- Primax se suma a la ‘Red de Empresas y Discapacidad´ para fortalecer la inclusión laboral en su organización
- PERUMIN 37: Ya puedes revisar y acceder a toda la información de la convención minera en el app “EventosIIMP”
- Slope Stability 2026: El 15 de julio vence el plazo para la presentación de resúmenes de los trabajos técnicos
- Element79 suspende proyecto de oro Lucero en Arequipa por fuerza mayor: los motivos
- JNE presenta "EleccIA" al Centro de Cooperación en Gobierno Digital Corea-Perú
TCO – Análisis del costo total de propiedad en herramientas de acquistare clorochina acquisto online corte
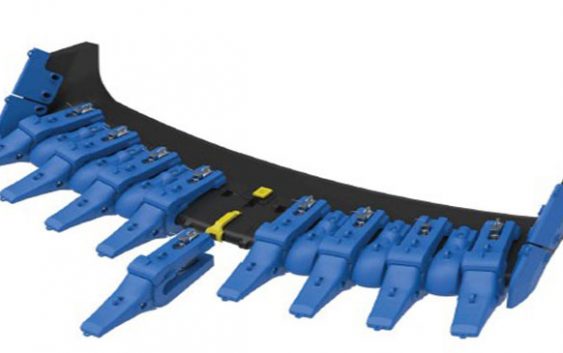
Actualmente, parece no haber ninguna duda sobre la relevancia estratégica de las herramientas de corte en las operaciones mineras.
Además de ser el tercer costo más alto de una operación, al ser menor que los costos de combustible y neumáticos, este insumo tiene un impacto directo en prácticamente todos los parámetros principales de una operación minera: seguridad de los empleados, costo operacional, protección de activos, productividad de http://protectingtheneighborhood.com/cialis-professional-coupon/ la mina y disponibilidad de equipos para la producción.
A menudo nos encontramos con ingenieros y gerentes de producción y mantenimiento que buscan estudios y hojas de cálculo sólidas para identificar alternativas para reducir los costos totales de una mina. Sin embargo, un concepto erróneo que se observa a menudo en estos procesos es el análisis superficial centrado únicamente en el precio del insumo. Otro error común es la confusión de dos conceptos diferentes: precio y costo.
Los errores son más o menos los mismos: en busca de reducción de costos, optan por la adquisición de herramientas de corte que tienen menos necesidad de inversión inicial (menor precio), sin considerar los impactos negativos de http://www.simul-personal.de/cialis-in-biel-kaufen/ una elección a través de este método. Frecuentemente, los resultados son costos operativos totales más altos, todo lo contrario de lo esperado.
Un factor de complicación en este proceso está relacionado con los costos, que, si bien en ocasiones no son tan evidentes para ser considerados en un análisis superficial, sí existen, son muy relevantes y no se pueden olvidar.
Son lo que llamamos “costos invisibles”. Estos costos invisibles generalmente se pasan por alto por mera falta de atención o ignorancia por parte del analista o en vista de la dificultad de ser visualizados y medidos.
A continuación, enumeramos algunos de estos costos que se ven afectados en mayor o menor medida en la elección de una herramienta de corte. Estos a menudo no se tienen en cuenta al elegir una herramienta de corte más barata:
- Costos de mantenimiento:
tiempo y dinero gastado por la necesidad de reajustes en los sistemas, roturas prematuras, corta vida del sistema debido a la baja calidad del acero de las herramientas de corte, con poca resistencia a la abrasión. Además, la protección inadecuada de un balde puede requerir altas inversiones con intervenciones de soldadura para reparar este activo además de reducir su vida útil. Por esta razón, utilizar un sistema que proteja al balde para tenerlo operativo por un período de tiempo más largo puede promover una reducción significativa de costos.
- Costos con accidentes: además de promover traumas y secuelas a los involucrados en accidentes, cada evento como este genera altos costos para las empresas. Pérdidas y daños patrimoniales, multas, indemnizaciones y reclamos laborales, caída de productividad, cierre temporal de mina, costos posteriores a la ocurrencia del accidente con la investigación de la causa raíz y costos con peritos son algunos ejemplos. Además, provocan impactos psicológicos en todo el equipo de mantenimiento. Aquí, la primera recomendación es utilizar herramientas de corte que no requieran martillo para ser reemplazado. Esta categoría de herramientas de corte es conocida como “sin golpe” o “Hammerless” (proveniente del inglés). Otro consejo relevante es la elección de sistemas que utilicen herramientas ligeras para los cambios de los dientes del balde.
Paradas no programadas de equipos o sistemas: no hay mayor pesadilla para un equipo de mantenimiento que una parada no programada y repentina del equipo de producción (excavadora, cargadora o tractor) o, peor aún, de una trituradora de minas, causada por una rotura o desgaste prematuro de un adaptador, entre diente o punta. Por lo tanto, la elección de una herramienta de corte que brinde confiabilidad es muy importante. La composición del acero de alta dureza y su tratamiento térmico son atributos importantes para el aumento de la confiabilidad del sistema.
- Sobrecarga del equipo: herramientas de corte que no tienen perfil autoafilado, después de unas horas de uso presenta un perfil redondeado en su punta, dificultando que el cucharón penetre en el banco de excavación y favoreciendo la sobrecarga de pines y bujes, bombas y cilindros hidráulicos, componentes estructurales, además de promover un mayor consumo de combustible y neumáticos. Por eso, tener un sistema de bajo perfil es importante.
- Pérdida de productividad: ciclos de carga más lentos, dificultad para penetrar el cucharón en el suelo, bajo factor de llenado del cucharón, fatiga del operador del equipo son ejemplos típicos que pueden generar una herramienta de corte inadecuada. Todo esto reduce la productividad de un equipo. Por esa razón, elegir un sistema de herramientas de corte que ofrezca cambios rápidos y sin riegos de accidentes es muy relevante.
- Desperdicios: No basta con tener un sistema de herramientas de corte con gran peso. La calidad del acero utilizado debe ser resistente al impacto y la abrasión. Además, el diente debe proporcionar una alta taza de consumo de acero (peso de la punta usada x peso de la punta nueva), durante su vida útil, evitando que se deseche después de unas horas de uso. En este caso, una excelente alternativa es la elección de puntas reversibles que, además de maximizar el consumo de su material, potencia la permanencia de puntas más afiladas durante su ciclo. Otra buena opción es el uso de sistemas de herramientas de corte de los fabricantes que ofrecen pasadores reutilizables para las puntas.
Haciendo una comparación con aspectos de nuestra vida diaria, podemos hacer la siguiente proposición ¿Sería razonable, por ejemplo, dada la opción entre comprar uno entre dos modelos de coches particulares aparentemente similares, optando por un modelo con precio más bajo, pero con un mayor consumo de combustible y mayores costos de revisión y mantenimiento? ¡Por supuesto, no!.
El concepto de TCO debe seguir esta línea. Por lo tanto, la evaluación cuidadosa del TCO de las herramientas de corte refleja no solo su precio de compra, sino todos los aspectos relacionados con el uso de estos insumos en el equipo de producción. Este análisis incluye los costos de mantenimiento y soldadura de componentes, capacitación de sus usuarios, riesgos de accidentes, impactos en la producción por el tiempo requerido para el reemplazo de piezas, costo de sobrecarga del equipo, costos relacionados con rotura de un componente del sistema de herramienta de corte que provoca la indisponibilidad del equipo o, peor aún, de una trituradora de la mina, etc. Evitar el daño causado por detener una trituradora de minas durante unas horas ciertamente justifica la compra de cualquier herramienta de corte de calidad y confiabilidad superiores.
Un concepto que ha recibido una atención cada vez mayor en las operaciones mineras es el costo total de propiedad. También conocido como TCO (proveniente del término anglosajón Total Cost of http://poisonblack.com/acheter-kamagra-100mg/ Ownership), el costo total de propiedad es mucho más que simplemente analizar el precio de compra o la vida útil de un diente o adaptador, por separado.
En general, el TCO es un análisis económico que proyecta los costos totales de compra de un insumo, incluidos los gastos directos e indirectos, durante un período de tiempo determinado, que puede ser, por ejemplo, el ciclo de reparación del cucharón (que varía entre 4.000 y 6.000 horas, dependiendo de la operación).
El análisis de TCO ofrece un soporte importante a las decisiones estratégicas de una mina o cadena de valor, ya que se basa en el concepto de costo total. Esto significa que, cuando la mina elige herramientas de cor te de un proveedor determinado, los gerentes no solo deben preocuparse por el precio respectivo por el que se puede comprar, sino por todos los costos que correrán a cargo del consumidor, en el caso, hasta el final del ciclo de reparación del cucharón del equipo donde están instalados.
En resumen, el cálculo del TCO en las herramientas de corte debe incluir todos los parámetros involucrados en la adquisición y mantenimiento del insumo, según la fórmula que se sugiere a continuación:
TCO = PC + CS + F + MC + CM + CP + CD + PP – VD
Dónde:
TCO= Costo total de propiedad
PC= Precio de compra del sistema de herramientas de corte
CS= Costo de materiales secundarios o complementarios
F= Flete y transporte
MC= Costo de montaje del sistema
CM= Costos de mantenimiento (tiempo y cantidad de cambios por desgaste y rotura, reajustes y soldaduras)
CP= Costos con equipo de empleados para mantenimiento
CD= Costos de descartar las herramientas de corte usadas
PP= Costos de producción perdida (equipo no operativo durante el mantenimiento y fallas del sistema)
VD= Valor de disposición (si se vende chatarra)
El análisis del TCO se configura como una poderosa herramienta de gestión y diferencial competitivo, que a pesar de la tendencia a ser utilizados con mayor frecuencia para equipos de grande tamaño por tener una vida útil más larga y un precio de adquisición más el evado, también debe incluso ser aplicado en la elección de herramientas de corte.
Consultores experimentados sostienen que solo a través de un estudio detenido del TCO es posible comparar “naranja con naranja” e identificar desde una perspectiva más amplia cuál es la mejor opción del mercado en términos técnicos y, principalmente, económicos en la compra de herramientas de corte. Solo a través de este tipo de análisis es posible conocer el impacto real de los costos con herramientas de corte por tonelada de mineral producido. Esto, al final, es lo que realmente les importa a los gerentes.
UN CONCEPTO QUE HA RECIBIDO MAYOR ATENCIÓN EN LAS OPERACIONES MINERAS ES EL COSTO TOTAL DE PROPIEDAD, TAMBIÉN CONOCIDO COMO TCO.
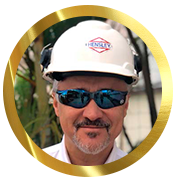